ボーディングスクール留学のメリットやデメリット、留学費用を紹介!高校生の留学先選びの手助けに
留学を検討する高校生やその家族にとって、ボーディングスクールは異なる教育体験を提供する選択肢の1つです。生徒は独立心や自己管理能力を養い、異文化間での交流や経験を通じて成長する機会を得ることができます。
ボーディングスクールとは?
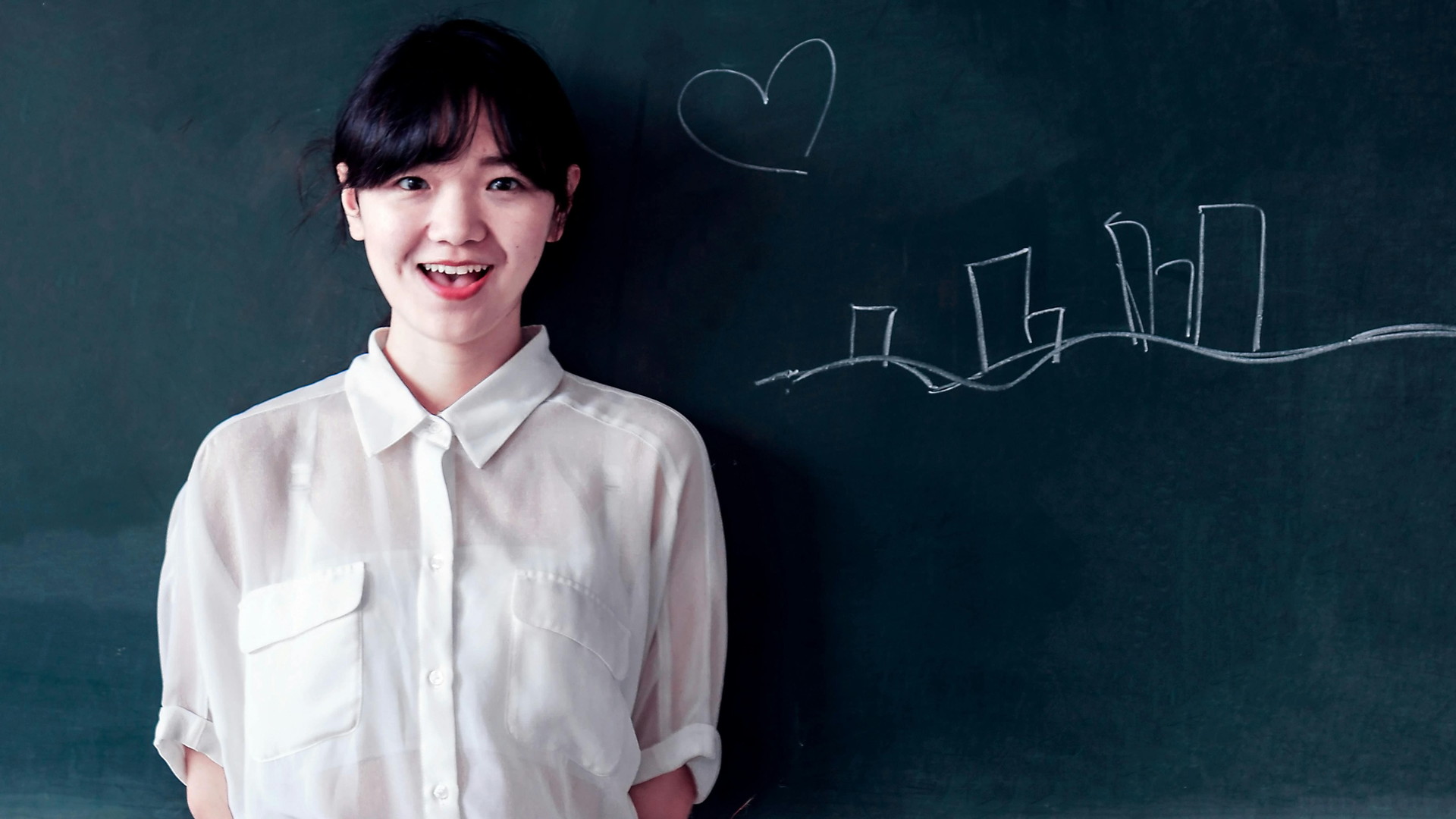
ボーディングスクールは、一般的な学校とは異なる、生徒が学校に寄宿して学ぶ教育機関です。こうした学校では、生徒たちは通常、週に数日または週末を含む数週間を学校で過ごします。これにより、学校は生徒の学習環境を管理し、その成績や生活様式に影響を与えます。ボーディングスクールの歴史は古く、中世ヨーロッパにまで遡ります。英国のパブリックスクール(私立学校)がその起源とされ、貴族の子弟に対する教育機会を提供してきました。しかし、今日ではボーディングスクールは世界中で見られ、異なる教育システムや文化のもとで多様な形態で存在しています。これらの学校の特徴の1つは、生徒が学校内で生活することです。生徒は通常、寮で過ごし、学習や生活の時間を共にします。そのため、生徒たちは同じ環境で生活することで、友情や共同生活のスキルを築くことができます。また、多くのボーディングスクールは厳格なカリキュラムを採用しており、生徒たちは学業に集中し、成績を向上させる機会を得ることができます。さらに、スポーツや芸術などの課外活動も豊富に提供され、生徒たちは多様な分野で自己表現する機会を得ることができます。
ボーディングスクール留学のメリット
ボーディングスクール留学には多くのメリットがあります。その中でも、最も注目すべきメリットの1つは、学習環境の充実です。ボーディングスクールでは、生徒たちは学校内で生活し、学業に集中することができます。この環境は、学習意欲や成績の向上に直結し、生徒たちが将来のキャリアに備えるための強固な基盤を築くのに役立ちます。また、ボーディングスクールでは生徒たちがさまざまな文化やバックグラウンドを持つ仲間と交流する機会が与えられます。このような多文化環境は、異なる視点や価値観を理解し、世界観を広げるための貴重な機会となります。さらに、異なる国や地域からの生徒たちとの交流は、国際的な視野を育み、国際的なネットワークを構築する手助けとなります。ボーディングスクールでは、生徒たちが自己管理能力や責任感を養う機会も豊富に提供されます。寄宿生活を送ることで、自己管理や時間管理、チームワークなどのスキルを磨くことができます。これらのスキルは将来のキャリアや社会生活において不可欠なものであり、ボーディングスクール留学を通じて身につけることができます。さらに、ボーディングスクールでは、豊富な課外活動やスポーツプログラ ムが提供されます。これにより、生徒たちは自分の興味や才能に応じて活動を選択し、多様な分野で自己表現する機会を得ることができます。このような経験は生徒たちの成長と自己実現に大きく貢献し、彼らの個性を伸ばすのに役立ちます。
ボーディングスクール留学のデメリット
ボーディングスクール留学にはいくつかのデメリットも存在します。まず挙げられるのは、家族や友人から離れることによる孤独感やホームシックです。寄宿生活を送るため、生徒は親や兄弟姉妹から離れ、新しい環境で自立しなければなりません。この適応期間にはストレスを感じることがあります。さらに、ボーディングスクールは一般的に高額な学費がかかることがあります。寄宿費や教育費、課外活動費など、多くの費用がかかるため、経済的な負担が大きい場合もあります。これは家計に負担をかけるだけでなく、生徒自身にもストレスを与える可能性があります。また、ボーディングスクールでは厳格な規則やルールが存在する場合があります。これは生徒たちにとってストレスの原因となることがあります。特に、自由な生活を送ってきた生徒にとって、規律の厳しい環境に適応することが難しい場合があります。さらに、一部のボーディングスクールでは、生徒同士や教師との関係において問題が発生することがあります。いじめやパワーハラスメントなどの問題が生じた場合、それが解決されるまでに時間がかかることがあります。これは生徒の心身の健康に悪影響を与える可能性があります 。これらのデメリットはボーディングスクール留学を検討する際に考慮すべき点です。しっかりとリサーチし、自分に合った学校を選ぶことが重要です。
ボーディングスクール留学の費用とは?
ボーディングスクール留学は高額な費用がかかることが一般的です。これは、寄宿費や教育費、食事代、課外活動費など、さまざまな費用が含まれるためです。以下では、ボーディングスクール留学にかかる主な費用について詳しく説明します。まず、ボーディングスクール留学には寄宿費が含まれます。これは、学校内で提供される宿泊施設や食事、生活用品などをカバーするための費用です。寄宿費の金額は、学校や地域によって異なりますが、一般的には月額数千ドルから数万ドルに及ぶことがあります。次に、教育費があります。ボーディングスクールでは高品質の教育が提供されるため、授業料は通常高額です。これには、学校の施設や教員の給与、教育プログラムの費用などが含まれます。教育費の金額は、学校の評価やカリキュラムの内容によって異なります。さらに、課外活動費もかかります。ボーディングスクールではさまざまな課外活動やクラブ活動が提供されるため、これらの費用も学費に含まれることがあります。例えば、スポーツ活動や芸術活動、ボランティア活動などがありますが、これらの活動には追加料金が必要な場合があります。また、教材や学用品、制服などの追加費用も 考慮する必要があります。これらの費用は、学校によって異なりますが、一般的には学期ごとに数百ドルから数千ドルかかることがあります。
ボーディングスクール選びのポイント
ボーディングスクールを選ぶ際には、さまざまな要因を考慮する必要があります。以下では、ボーディングスクールを選ぶ際のポイントについて詳しく説明します。まず、学校の評判や歴史を確認することが重要です。良い評判を持つ学校は、教育の質や学生の満足度が高い傾向があります。また、歴史のある学校は伝統や安定感があり、信頼性が高いとされています。次に、カリキュラムや教育方針を確認しましょう。自分の興味や将来のキャリア目標に合ったカリキュラムや教育方針を持つ学校を選ぶことが重要です。また、特別なプログラムや取り組みがある学校もありますので、それらを活用できるかどうかも考慮しましょう。また、学校の施設や設備も重要なポイントです。快適な寄宿施設や最新の教育設備が整っている学校は、より良い学習環境を提供できる可能性があります。また、スポーツ施設や芸術施設など、興味や趣味に合った施設があるかどうかも確認しましょう。さらに、学校の地理的な位置や環境も考慮しましょう。自然豊かな環境や文化的な都市で学ぶことができる学校は、留学生活をより豊かなものにする可能性があります。また、地理的な立地や気候によって異なる文化や生活 環境を体験できるかどうかも重要な要素です。最後に、学校の入学条件や奨学金制度も確認しましょう。入学条件や奨学金の有無は、留学を検討する上で重要な要素です。自分の学力や能力に合った学校を選ぶことが、成功するための第一歩となります。
まとめ
ボーディングスクールを選ぶ際には、様々な要素を考慮する必要があります。メリットとデメリット、費用、選び方のポイントを総合的に考えることで、自分に合った最適な選択ができるでしょう。留学先を選ぶ際には、自分の目標や希望に合った学校を選ぶことが重要です。十分な情報収集を行い、慎重に検討することで、充実した留学生活を送ることができるでしょう。